Introduction
Both Design Review (DR) and Design Qualification (DQ) are early lifecycle verification activities in the C&Q process. They support leveraging later in Installation Qualification (IQ) and Operational Qualification (OQ) by ensuring the foundation (i.e., the design) is solid and compliant.
They also reduce rework and project risk by catching design flaws before construction or procurement begins.
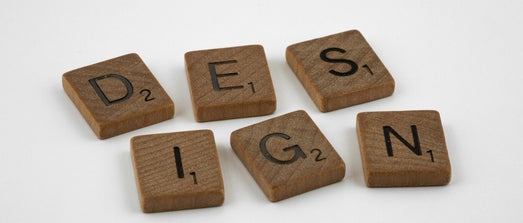
Objective of Design Review
Design reviews provide confidence that the design outputs are aligned with the User Requirements Specification (URS) and the risk control strategies developed during the System Risk Assessment. A design review is defined as a planned and systematic evaluation of specifications, design, design development, and any continuous improvement changes, conducted as appropriate throughout the manufacturing system lifecycle.
These reviews assess design deliverables against applicable standards and requirements, identify potential issues, and propose appropriate corrective actions. Design reviews encompass both quality-critical and non-critical elements of the system design.
Roles and Responsibilities
Cross-functional project team is involved throughout the design process to ensure the requirements of product, process, GMP and regulatory are included. Subject Matter Expert should be included who has experience and knowledge of the process, equipment, control strategies and facilities that meet the URS, functions efficiently to produce quality products in consistent manner. Quality representative should be included for direct impact system to ensure all quality requirements are met and to facilitate review or approval of DQ.
Design Review Process
Design documents should be circulated to design team prior to the design review by project manager or design lead. Senior management from Quality, operations and production will ensure the presence of representatives with appropriate experiences and knowledges for the DR.
Project team will define the design review method based on system type, size and risk. This method will be documented in applicable plans i.e. project execution plan, Commissioning & Qualification plan etc.
ICH Q9 principle should be used for the documentation of DRs and this documentation can be the form of engineering meeting minutes or notes. DRs can be more detailed for highly critical novel systems.
For off-the-shelf equipment, DR is based on the complexity and/or risk to the system or facility operation and to the quality. Vendor documentations are used in review process and a technical vendor representative could attend during the DR as required.
DRs are done for both engineering and quality requirements where engineering aspect verifies operations, maintenance and the safety of the system. The quality focuses on the compliance elements where Critical Attributes or Critical design elements of the system design affect product quality, also to compliance of regulatory requirements.
Design Review Outcome
The DR project team must effectively document and share DR results and manage any resulting changes, ensuring the design remains appropriate and fit for purpose. The design team must report any design-related issues to management.
The overview of DR process is provided in the flow diagram of Figure 1:
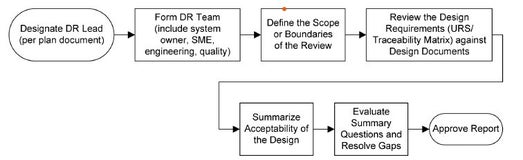
Figure 1: Design review process flow
Objective of DQ
1. Verify the design meets the quality user requirements
2. Verify that the Design control risks associated to product quality and patient safety as identified through System Risk Assessment
3. Verify the Critical Attributes and Critical Design Elements required to control risks and meet product quality, patient safety
DQ Prerequisites
1. Approved URS
2. Functional requirements for automated systems
3. System risk assessments with identification of Critical Attributes (CAs), Critical Design elements (CDEs) and procedural control to mitigate risks
4. Completed DRs, including verification of any design issues that impact CAs, CDEs, CPPs and CQAs are resolved and included in final design
DQ Process
DQ is the documented process for the review and approval of the final system design to verify the followings:
1. All process and product requirements in URS are incorporated into the design
2. Quality and regulatory requirements are incorporated
3. Any changes in design are reviewed for CAs and CDEs
Planning documents should define the approach for performing the DQ. One DQ may be performed for small projects after all the design is completed. For larger projects, DQ can be broken into several areas or functions, with the DQ performed when each design is completed.
It is not mandatory regulatory requirements to have a formal protocol for DQ these should be defined i.e. plan for conducting DQ, scope of the DQ and Quality approval of the DQ. A traceability matrix can be used to document traceability of design requirements i.e. CAs, CDEs, CPPs to the CQAs.
DQ Report
The DQ report should include:
-
Documentation of necessary risk reviews showing integration of design control elements to ensure quality manufacturing.
-
Identification of each CDE that addresses potential process failures.
- Description of each CA and any supporting CDEs in terms that are verifiable mainly through inspection and testing
-
Verifiable descriptions of each CA and related CDEs, primarily through performance testing.
The final report must confirm the design is suitable for its intended purpose and be approved by Engineering, Manufacturing, and Quality unit representatives. Figure 2 provides an overview of the DQ process.
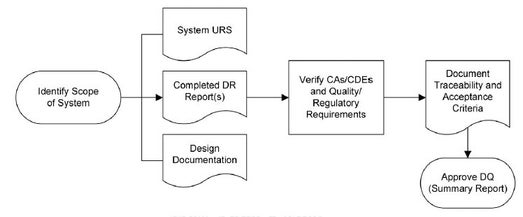
Figure 2: Design Qualification process flow
Add comment
Comments